- Home
- Blogs
07.05.2021
Core XR7 Launch und Interview: Fragen an Kite-Entwickler Frank Ilfrich
Hier gehts zum neuen Core XR7
Es ist endlich wieder so weit: Core Kiteboarding bringt einen neuen Kite auf den Markt - den XR7 Kite. Zum Launch bieten wir dir etwas Besonderes: Wir haben den XR7 nicht nur auf Lager, sondern bieten dir auch einen Blick hinter die Kulissen: Wir haben Frank Ilfrich, den Leiter der Entwicklung von Core und Carved, zum Interview getroffen und viele spannende Details erfahren über die Entwicklung des XR7, welche Neuheiten dich erwarten, welche Herausforderungen es gab und worauf Frank als verantwortlicher Kite-Designer besonders stolz. Da Core seit Jahren eine super hohe Fertigungsqualität aufweist werfen wir auch darauf einen Blick. Als Fan von Core solltest du das nicht verpassen… viel Spaß beim Lesen!
Um dich schon mal für das Interview in Stimmung zu bringen, hier das kürzlich veröffentlichte Produktvideo von Core zum neuen XR7!
Interview mit Frank Ilfrich, Head of R&D, Core Kiteboarding & Carved
Frank… bitte gib uns eine kurze Einführung dazu wer du bist und was du machst!Moin, ich bin Frank Ilfrich, Kitedesigner und Head of R&D bei CORE. Ich kite seit über 20 Jahren und arbeite seit 2005 für CORE und CARVED. Mir macht Kiten Spaß – egal ob auf dem Twintip, Directional oder Foil. Da hier auf Fehmarn selten eine gute Welle steht, kommt das Directional jedoch meist im Urlaub oder auf Test-Reisen zum Einsatz.
Kannst du uns einen Überblick dazu geben, wie die Produktentwicklung von Kites bei Core abläuft?
Jedes Produkt durchläuft drei Entwicklungsphasen: von der Analyse-Phase, bei der wir analysieren was das Produkt können muss, für welche Zielgruppe es passen soll usw. hin zur Design-Phase und abschließend in die Test-Phase. Grundsätzlich unterscheidet sich der Entwicklungsprozess, wenn man ein neues Modell entwirft oder eine bestehende Reihe fortführt.
So haben wir bei der Entwicklung des XLite den Nexus als Basis genommen, da dieser bereits in vielen Aspekten richtig gut funktioniert hat. Von dort aus sind wir dann gestartet und haben so viele Änderungen vorgenommen, bis wir alle Anforderungen an den idealen XLite erfüllt haben – sprich er tut genau das was er soll und ist dazu auch leicht zu bedienen und hebt sich ausreichend von anderen Kites ab. Bei Kites, wie dem XR, den wir seit Jahren fortführen steht zu Beginn der Analysephase die Auswertung des Feedbacks, welches wir von unseren Händlern, Importeuren und Schulen, Teamfahrern und Endkunden über die Laufzeit des Vorgängermodells erhalten haben. Dieses Feedback ist für uns viel Wert. Zusätzlich hat man als hat man als Entwickler natürlich bereits auch Ideen im Kopf, die man angehen möchte und versuchen möchte zu verwirklichen. Als weiterer Faktor sind dann außerdem neue Materialien zu berücksichtigen, die bestimmte Neuerungen beim Produkt erst möglich machen und andersherum auch Anpassungen fordern. Aus diesen Faktoren werden die Anforderungen an das nächste Kite-Modell definiert und es geht in die Design-Phase.
In der Design-Phase gilt es dann diese Anforderungen in unseren Produkten umzusetzen. Durch die jahrelange Arbeit wissen wir, an welchen Stellschrauben wir drehen müssen, um bestimmte Eigenschaften herauszukitzeln. Wir entwerfen dann verschiedene Modelle, bspw. A, B und C in unserer Design-Software, schicken das in die Fertigung und 10-12 Tage später haben wir unsere Prototypen hier auf Fehmarn zum Testen.
In der Test-Phase treten dann die Kites A, B und C gegen das aktuelle Modell an und werden anhand einer bestimmten Anforderung aber natürlich auch insgesamt bewertet. Ich hole mir dann das Feedback von Teamridern aber auch ganz normalen Kitern ein. Produkte zu testen ist wirklich ein anstrengender und zeitaufwendiger Prozess, richtig Testen muss man lernen. Neben den erfahrenen Testern lass ich aber auch immer Leute an die Prototypen, die die Produkte einfach ganz normal benutzen und mir ungefiltert Feedback geben. Sobald wir dann zufrieden sind, geht der Kite in die Produktion.
Auch wenn der Kite dann bereits unsere Erwartungen mehr als erfüllt, ist es für mich als Designer so, dass man manchmal immer noch das Bedürfnis hat diese eine Stellschrauben dann doch nochmal anzufassen oder den Trimm nochmal zu überarbeiten etc. Oft hat man dann so ein Bauchgefühl, dass dies nochmal etwas verändern könnte, aber irgendwann muss man ja dann auch zum Ende kommen. Ich mach das dann so, dass ich alle Ideen, die ich nicht mehr voll austesten konnte, dann in den ersten Prototypen der nächsten Generation mit einfließen lasse. Die Entwicklung geht dann nahtlos weiter.
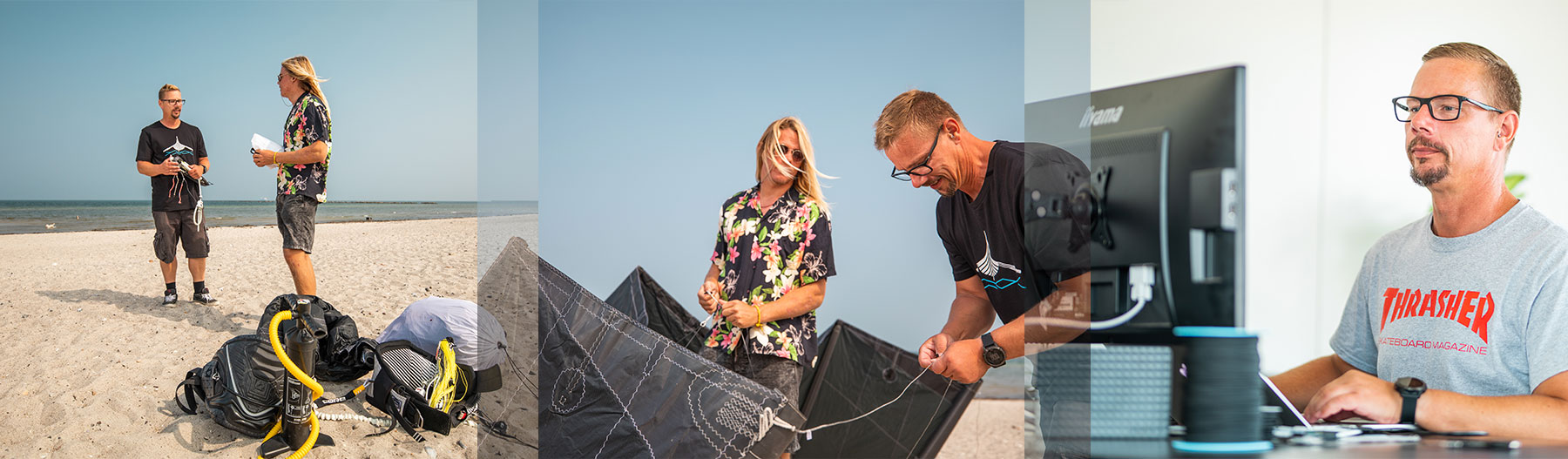
Inwiefern spielen technische Hilfsmittel zur Erfassung von Daten eine Rolle beim Testen von Prototypen?
Wir verwenden bei unseren Tests einfachere Geräte wie bspw. die WOO und GPS-Tracker, um Sprunghöhen oder auch die Höhelauf-Eigenschaften zu vergleichen. Es gibt natürlich auch Methoden, um bspw. den Leinendruck etc. zu messen. Wir hatten damals ein Projekt dazu gestartet mit der Uni Berlin. Außerdem simulieren und messen wir auch Strömungslinien bei unseren Kites. Jedoch muss man ganz klar sagen, dass all diese Geräte und Simulationen den Spaß einer Session auf dem Wasser nicht einfangen können und darum geht es letztlich. Auf dem Papier sind dann die Leistungsdaten von einem Modell zwar etwas besser, aber das Zusammenspiel der ganzen Faktoren ist so komplex, dass man dies einfach nicht simulieren kann – kein Computersystem der Welt kann das bisher. Der Mensch bleibt daher für uns das beste Messinstrument.
Der XR blickt ja inzwischen auf stolze 12 Jahre Entwicklungsgeschichte zurück und damit ja auf hunderte Prototypen. Ich schätze mal, die größten Entwicklungsschritte liegen daher heutzutage eher beim Material. Was hat sich da getan?
Beim Material hat sich in den letzten zwei Jahren allgemein viel getan am Markt und wir verwenden beim XR7 zum ersten Mal das neue CoreTex 2 Tuch. Die Entwicklung dieses neuen Tuchs hat insgesamt drei Jahre in Anspruch genommen. Beim CoreTex 2 haben wir uns bewusst auf das Coating des Tuchs konzentriert, da es in dem Bereich gravierende Unterschiede gibt bzgl. Haltbarkeit, Dehnung, Reißfestigkeit usw. Für mich als Designer oder auch als Hersteller birgt ein neues Material aber auch immer ein gewisses Risiko. In diesem Bereich haben wir auch Bock neue Wege zu beschreiten und vlt. auch schon mehr im Köcher als wir preisgeben, aber müssen dort auch immer sehr vorsichtig vorgehen und alles Neue natürlich ausführlich testen.
Der XR hat eine besonders breite Fanbase – vom Big Air Piloten mit +30m Sprüngen zu Kite-Schülern, die gerade ihre ersten Meter fahren – ist es besonders anspruchsvoll oder auch aufwändiger einen Kite mit einer so breiten Fanbase zu verändern oder zu verbessern, als bspw. einen XLite oder Section aus der Specialized Series?
Bei unseren Specialized Produkten ist es im Prinzip schon etwas anderes, weil der Kite genau auf ein Einsatzgebiet zugeschnitten ist. Dort sollen die Produkte ja aber dann eben auch absolute Topleistungen bieten, was natürlich auch wieder eine große Herausforderung darstellt. Trotzdem müssen auch diese Produkte von jedermann beherrschbar bleiben - den Impact mal ausgenommen ;-)
Bei Kites aus der Universal+ Series wie dem XR gibt es da oft eine breitere Palette an Anforderungen, da die Kites für mehrere Disziplinen und Kiter*innen geeignet sein müssen. Dazu kommt, dass dann diese Leistung eben auch leicht abrufbar sein muss. Als Designer möchte man natürlich auch, dass sich das Produkt weiterentwickelt, auch da man sich selbst weiterentwickelt, genauso wie die Kunden. Aber natürlich gibt es auch immer Personen, die neu in den Sport dazu kommen. Zum einen kann man dadurch als Designer vielleicht nicht immer alles umsetzen, was man sich so gewünscht hat. Zum anderen ist es jedoch auch gut, da man so immer wieder herausgefordert wird, den Kite mit mehr Leistung auszustatten, aber immer noch einfach zu benutzen ist und seinen Charakter beibehält. So hatten wir beim XR bereits Prototypen, die bspw. größere Leistungsspitzen in der Sprunghöhe erreicht haben, jedoch konnten diese Leistung dann nur wenige, sehr gute Fahrer*innen abrufen und wir haben uns dann im finalen Modell dazu entschieden, den Prototyp umzusetzen, der einfacher zu springen ist. Als Designer sehe ich da absolut die Kundenperspektive: Man hat einfach dadurch mehr Spaß auf dem Wasser. Daher muss man immer wieder abwägen, welche Richtung man verfolgen möchte, aber bisher haben wir diesen Spagat immer sehr gut geschafft.
Welche Vision gab es zu Beginn für den neuen XR7 und wie wurde darauf hingearbeitet?
Klares Ziel war es beim XR7 nicht nur die Leistung zu steigern, sondern auch die Drehgeschwindigkeit und Lenkpräzision zu steigern. Der XR Kunde wächst ja auch mit dem Kite mit und Formate wie der KOTA und Rider wie Janek Grzegorzewski pushen das Limit das von Kites wie dem XR inzwischen erwartet wird ständig weiter. Konkret war es klarerweise auch ein Ziel, das verbesserte Flugtuch CoreTex 2 im XR7 zu verbauen, da es mehr Leistung und mehr Stabilität ermöglicht.
Neue Materialien bedeuten immer auch Anpassungen ans Kite Design. Wenn ein Parameter wie das Flugtuch geändert wird, muss man an verschiedenen Stellschrauben drehen um das Kite Design an das Material anzupassen. Im Falle von CoreTex 2 z.B. gewinnen wir an Leistung und Flugstabilität durch ein neues Coating, aber da damit einhergehende geringere Dehnung im Flugtuch bedeutet auch weniger Verwindung des Kite beim Lenken. LE- und Strutdurchmesser, Bridle Setup usw sind hierbei Möglichkeiten Einfluss zu nehmen und natürlich auch das angestrebte geringere Gesamtgewicht.
Als führender Kite in der weltweiten Woo-Rangliste wollen wir natürlich mit dem XR auch weiterhin ganz oben mitspielen und seine Topleistungen zu verbessern. Dafür versuchen wir auch diese immer weiter voranzutreiben, ohne Abstriche im einfachen Handling in Kauf nehmen zu müssen.
Auf welche Neuheiten können wir uns beim XR7 freuen und welche Auswirkungen haben diese für ambitionierte Rider und auch Einsteiger*innen? Auf welchen Aspekt bist du als Entwickler besonders stolz?
Das neue leistungsfähigere CoreTex 2 und das reduzierte Gewicht des XR7 sind wohl die am deutlichsten spürbaren Neuerungen. Mehr Power trotzdem spielerischer, beim Freeriden, in der Welle aber auch bei Big Air und Kiteloops wirkt sich das positiv aus.
Natürlich freut es mich, dass wir aktuell den WOO Hochsprung Rekord halten, aber mindestens genauso freue ich mich über zufriedene Cruiser und Freerider, die eine gute Zeit auf dem Wasser haben, oder sogar Anfänger die das Kiten erlernen mit dem XR. Ich denke es gibt nicht viele Kites die so eine breite Zielgruppe bedienen können.
Welche Herausforderungen gab es bei der Entwicklung des XR7 und wie wurden diese bewältigt?
Der neue Materialmix und der Anspruch immer alles besser zu machen, ohne eine Eigenschaft zu verschlechtern ist die zentrale Herausforderung. Oder vereinfacht gesagt, einen spannenden Kite zu entwickeln der sich einerseits frisch aber trotzdem bekannt anfühlt.
Wurde die Entwicklung - und falls ja wie - durch Corona beeinträchtigt (bspw. Reisebeschränkungen, Verfügbarkeit von Materialien etc.)?
Klar hat die Situation viele Sachen nicht gerade einfacher gemacht. Glücklicherweise durften wir ja im Frühjahr auch weiterhin in Deutschland testen und die meisten unserer Lieferanten konnten weiterarbeiten, aber es hat schon vieles erschwert und Zeit und Nerven gekostet. Die Feuerprobe in Kapstadt hat der XR7 dann auch sehr erfolgreich bestanden.
Bei der letztes Jahr eingeführten Sensor 3 Bar gab es durch Corona deutlich mehr Stolpersteine wie Materialverfügbarkeit, Lieferverzögerungen usw.
Die Kites von Core bestechen seit Jahren unter anderem durch hohe Fertigungsqualität. Kannst du mir mehr erzählen zur Produktion und wie das erreicht wird? Wir sind sehr glücklich und stolz, dass wir so lange und erfolgreich mit unserer Produktion zusammenarbeiten. 2005 haben wir von der Pieke auf die Produktion mit aufgebaut und wirklich viel Pionierarbeit in der Fertigung geleistet. Zu Beginn war die gesamte Produktion daher auch noch recht einfach gestaltet, aber inzwischen ist dort ein sehr hoher Professionalisierungsgrad eingetreten. Die komplette Fertigung ist ISO-zertifiziert, alles wird im Prozess durch Bar-Codes festgehalten und durch die jahrelange Zusammenarbeit und Erfahrung wurde dort in der Produktion ein enormes Wissen aufgebaut. Wenn ich dort Design-Ideen vorschlage, können die dort direkt darauf eingehen und mir Feedback dazu geben.
Nach wie vor bin ich sehr regelmäßig auch vor Ort und laufe die komplette Produktion mit und schau mir an, wo bspw. neue Arbeitsschritte entstehen oder wie neue Verarbeitungsmethoden oder Maschinen eingesetzt werden und erhalte darüber auch wieder Eindrücke, die ich in meine Arbeit mit einfließen lassen kann.
Wir dürfen uns daher glücklich schätzen als Teil der Familie gesehen zu werden und diese Einstellung und Liebe zum Detail sorgt für hohe Qualität und Verlässlichkeit. In der Produktion geben beide Seiten ihr Bestes dieses Qualitätsniveau ständig zu verbessern. Abgesehen davon herrscht in der Produktion auch echt ein super Betriebsklima, die Mitarbeiter fühlen sich dort wohl, es wird gelacht und Musik gehört und die Mitarbeiter arbeiten gerne dort – manche kenne ich nun bereits seit 15 Jahren und die sind über die Zeit vom Näher zum Abteilungsleiter aufgestiegen usw. – das alles zeigt sich letztlich auch in der Qualität.
In der Kite-Industrie kommt es aktuell immer wieder zu Lieferengpässen… Wie sieht die Verfügbarkeit beim neuen XR7 aus? Kann jeder, der den neuen XR7 fliegen will, sich den Kite direkt bestellen oder müssen die Kunden sich auf Wartezeiten einstellen?
Wir sind in der glücklichen Lage aufgrund unserer Einkaufsstrategie und unserer Designphilosophie einen guten Bestand an Materialien zur Kiteproduktion zur Verfügung zu haben. Weniger Tuchfarben helfen in dieser Situation natürlich auch ;-)
Gehen wir mal davon aus, der neue XR7 ist raus und die Teamfahrer haben sich mittlerweile auf den neuen Kite eingeschossen und ein fetter Sturm taucht in der Vorhersage auf… welche Höhen können wohl mit dem XR7 erreicht werden? Gibt es schon Wetten im Hause Core oder innerhalb der Teamrider?
Die Rankings haben in den letzten Jahren eine besondere Dynamik bekommen und Teamrider aller Brands sind motiviert und battlen sich mit ihren Teamkollegen und Freunden. Viele machen es aber aus Spaß, es geht mehr um den Adrenalinrausch und die Ergebnisse sind eine Begleiterscheinung. Ich weiß, dass die Mädels und Jungs sich darauf nicht speziell vorbereiten, sondern wenn es passt einfach Gas geben.
Da schlummert noch viel verstecktes Potential, gerade auch materialtechnisch, trotzdem ist natürlich die Tagesform des Riders der entscheidende Faktor. Die Tage an denen 30m+ möglich sind, sind auch nicht so häufig, da müssen schon viele Faktoren zusammenkommen – ich bin also sehr gespannt!
Super – vielen Dank für deine Zeit und dass du diese Einblicke mit uns geteilt hast!
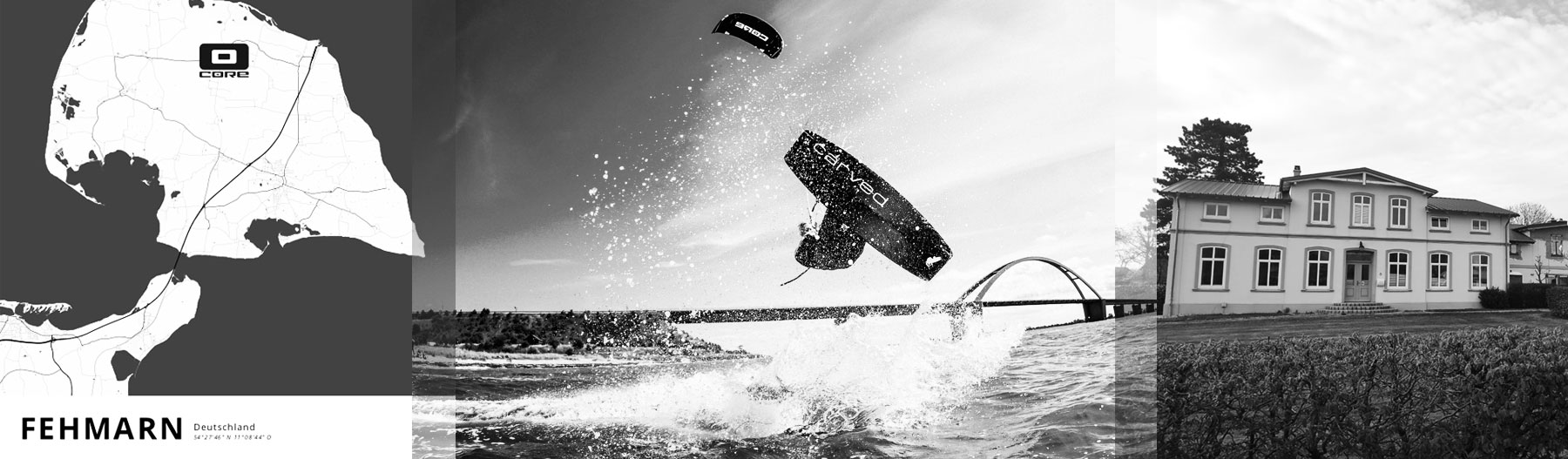
Warenkorb
Zwischensumme | € 0,00 |
Versandkosten NL | € 0,00 |
Gesamt (incl 0% MwSt.) | € 0,00 |
Sie haben keine Produkte in Ihrem Warenkorb
Weißt du nicht, wo du anfangen sollst?
Lassen Sie sich vom Kundendienst beraten